When a lace maker is preparing to plate a new lace, she creates some stock of split threads and saves it using accessible bearers including different spools and even cardboard strips. Flat strips are undesirable since the thread keeps tracks of bends.
On this reason cylindrical spools are preferable but they are not manufactured for lace makers in Russia. It is pity but there are no standards for lace thread spools. In that case the third operation is necessary to rewind thread. Consequently an additional contrivance is needed to accelerate rewinding and escape excessive touching to thread by fingers.
[wp_ad_camp_1]
As soon as there is no satisfactory decision of the problem, one is to solve two tasks:
- – to select the suitable spools for thread saving;
- – to invent a contrivance for rewinding threads from stationary intermediate spools to the saving spools.
Both tasks are to be decided by common efforts: a lace maker offers her own standard for the saving spool and a designer invents a contrivance fit to the spool.
Authors of the book decided to use a plastic package applied in homoeopathy as mass production. It is the cylindrical capsule with 22 mm (? 0.9 inch) in diameter and 39 mm (? 1.5 inch) in length. Three operations are needed to transform a capsule to the spool:
- – delete a lid;
- – make a hole in the bottom with an awl; it is necessary to set the spool at the rewind device;
- – set on the capsule a steel hair-pin (Fig.3.24); it is useful to attach the thirst coil on the spool.
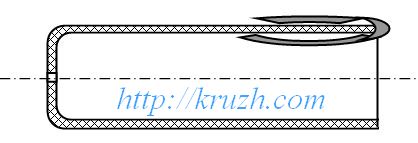
Ii is recommended to shorten a little the hair-pin. Of course one may not use the hair-pin, winding 2-3 start coils of the thread.
The rewinding operation is very simple itself but one is to pay attention on many hard restrictions:
- – uniform arranging of coils;
- – constructive attachment of two units intended to split and rewind thread;
- – keeping the special trajectory of thread going from the intermediate spool to the saving spool;
- – quick setting of the empty spool and quick taking it down after rewinding.
- – invent a contrivance to rewind threads from stationary intermediate spools to the saving spools.
All mentioned above demands can be satisfied with the following units:
- – an unit to set the empty spool for rewinding;
- – a reducer that lowers rate of gyration from the fly-wheel to the sheave of the mechanism laying coils;
- – a transformer of gyration to swaying movements of guiding fork.
Cinematic scheme of the contrivance contains two units:
- – reducer and the spool holder (Fig.3.25);
- – transformer of movement direction;
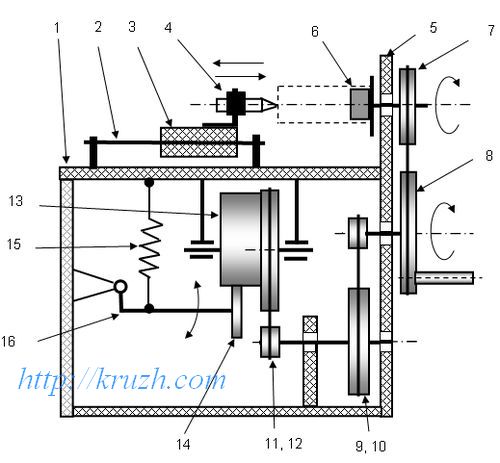
The bearing center 1 is set oh the base 2 that moves along guiding rods 3 attached to the platform 4.
Three gyration axes are set at the vertical platform 5. The spool chuck 6 and the sheave 7 are at the first axe. The sheave 7 and the fly-wheel 8 are joined as a belt pair that enlarges gyration rate.
The fly-wheel 8 and the sheave 9 are at the second gyration axe. The third axe carries the sheaves 10 and 11. Two pairs 9-10 and 11-12 reduce gyration rate of the fly-wheel.
The eccentric disk 13 is set on the sheave 12. The roller 14 is pressed to the shiver rim with the spring 15. The lever 16 drives the mechanism of laying coils on the spool.
The bearing center 1 is pulled right with a spring that is not shown on the scheme.
When the empty spool is being set, the bearing center is pulled left and open part of the spool is put on the chuck. The spike of the center is fixed at the spool bottom. The spool and the chuck rotates together due to the tight fit.
All the axes are set with ball bearings at the vertical platform 5. The rest axes need no ball bearings since their gyration rate is very low and they are slightly loaded.
Many details of the contrivance are made of ply-wood including all platforms, the sheaves 7-8 as well the sheave 12. The sheaver 10 is a ready roller with a ball bearing pressed into it. The wheels 9-11 and the eccentric disk 13 must have the ideal cylindrical surface.
Periodical swaying of the lever 16 transforms into reversible movements of the guiding fork (Fig.3.26).
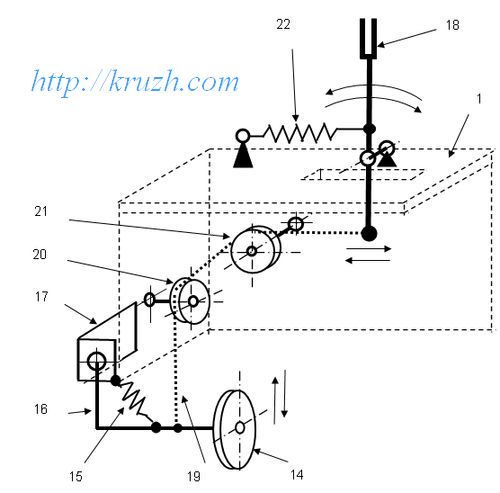
The lever 16 is attached to the bracket 17 with a hinge and is permanently pulled upward with the spring 15. In so manner the tight contact is provided between the roller 14 and the eccentric rim.
The lever 16 is tied to the guiding fork 18 with the cord 19 that goes through the rollers 20 and 21 set on the walls of the contrivance. The fork 18 is permanently inlined left with the spring 22.
When the eccentric drives the roller 14 downward, the cord 19 inclines the guiding fork right. When the roller 14 can move up, tension of the cord 19 becomes weak and the spring 22 inclines the fork 18 left.
At one revolution of the eccentric the fork 18 does the total cycle of inclination and the split thread lays twice along the spool.
Rollers 20 and 21 that changes direction of cord are standard spools for sewing machine.
Deviation amplitude of the guiding fork 14 depends on the position of point where the cord 19 is tied to the fork. The swaying becomes larger when the point moves nearer to the gyration axe. The position of the extreme coils of thread depends on the phase position of the guiding fork 14. The position is being corrected by means tension of cord.
Real contrivance one can see on Fig.3.27 … Fig,3.29.
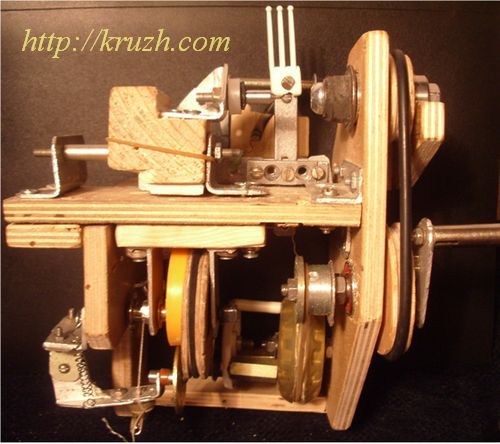
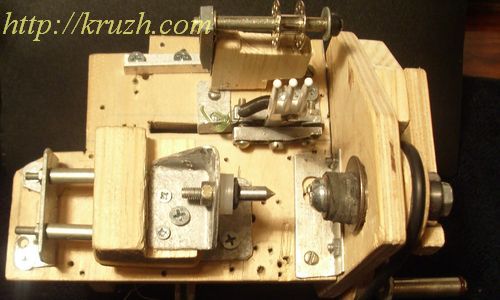
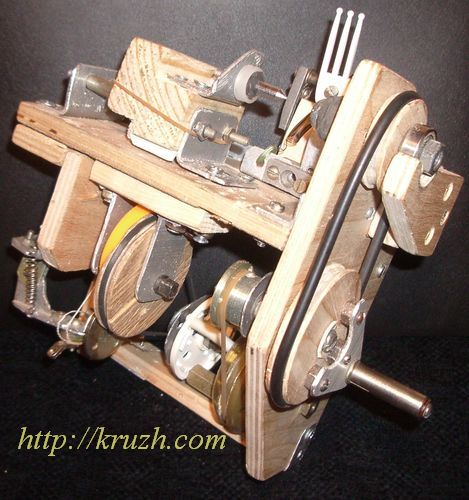